I toured the huge £500m Amazon warehouse in Sutton Coldfield - here’s how it’s shaping up for Christmas
and live on Freeview channel 276
The huge new £500m Amazon centre in Peddimore, Sutton Coldfield, is up and running in time for Christmas.
As Business Editor at the Express and Star I was invited to take a look around the 547,000 sq ft fulfilment centre - bigger than seven football pitches - which is not yet working at full capacity - but is shipping out goods to customers. The first item sent out was a box of ink cartridges for a printer. The team is likely to be super busy with Christmas on the way.
Advertisement
Hide AdAdvertisement
Hide AdThe enormous centre - which has power-generating solar panels on its roof and is logistically well placed near the M42 and M6 - has a total of 1,400 employees, growing to 2,000 people within three years. Its arrival has coincided with the imminent closure of Amazon’s Rugeley fulfilment centre. Amazon insists all 1,000 employees have been offered roles at the new base or other Amazon buildings.
"Some of the Rugeley team have already started here," says site manager Celia Syme, who arrived in the Midlands from Scotland during the pandemic. "For some, it’s closer to their home. Hopefully a high number will take up roles."
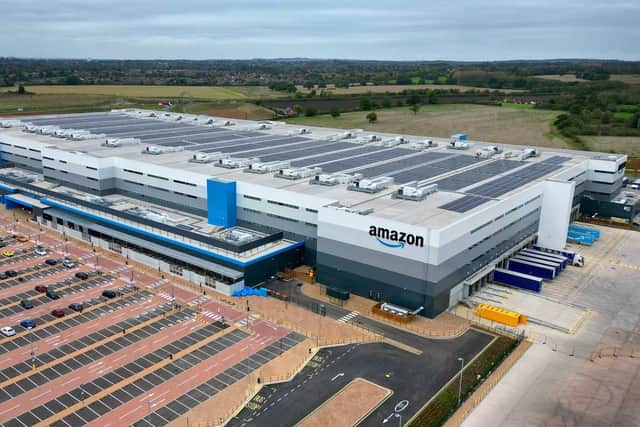
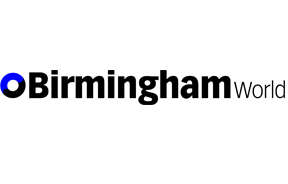
Bosses say the centre has created 400 additional new jobs for the West Midlands region, including teams of engineers, HR and IT professionals through to health and safety, finance specialists and operations managers, as well as the teams who pick, pack and ship customer orders.
Those staff are greeted by signs such as ‘Welcome Amazonians’ and ‘Welcome Pioneers’ on their arrival at work, I noticed, as I headed to the site for an exclusive look around. Amazon has faced criticism and plenty of bad press in relation to both working conditions and pay. Indeed, staff at one of the company’s receive centres, in nearby Coventry, have just announced a new round of strikes.
Advertisement
Hide AdAdvertisement
Hide AdBut, here, at least on this tour, I was struck by manager Celia’s enthusiasm and interaction with the team around her while leading me around. I’m told, by PR Manager Neil Williams, ahead of the visit that the technology in the centre ‘provides a real wow factor’ but that the importance of the team working there should not be under-estimated. "You need people," he adds.
And, as we walk around – you certainly get your steps in for the day – personable Celia is keen to stress the significance of her team. "The connection I have with the team is hugely important," she says. "If you invest time in trying to get to know people then it lays a strong foundation that you can build on.
"I want people to come to work and feel valued and feel a sense of purpose. It’s important for the team to get that human connection with their leaders. That, and connecting with each other, will be key to creating a positive environment here."
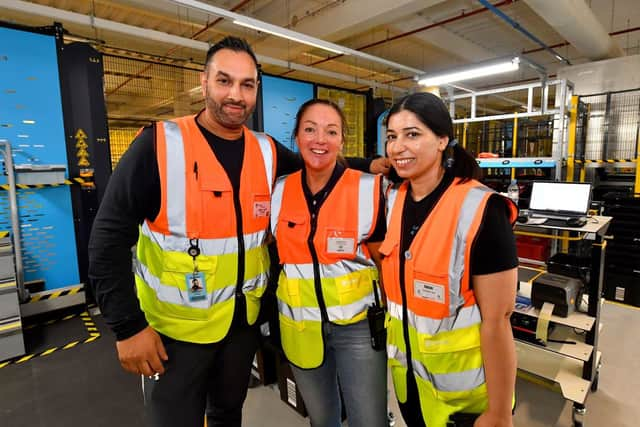
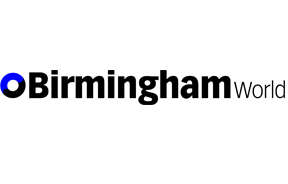
Slick operations at the Amazon warehouse in Sutton Coldfield
But what of the process? The set up is a terrific example of precision and detail in action. It’s a slick operation, where employees work alongside an army of wheeled, robotic machines, busily picking up goods in preparation for dispatch.
Advertisement
Hide AdAdvertisement
Hide AdOur first stop off in the factory is the ‘in-bound’ area where products come in. More than 50 per cent of the items you see in any centre of the Amazon Network are from other businesses – international firms, SMEs or an individual.
We chat about the impact of online retailers on the high street but Celia believes there is a place for both. "I like physically going into a store," she says."But then sometimes you need a particular something ‘for tomorrow’ and it’s that convenience.
"I think it’s important to say that we support a lot of smaller businesses here. For example, I love the stories of people creating home-made cards in their bedroom and then selling them through Amazon."
What happens when an item arrives at the Amazon warehouse in Sutton Coldfield?
Products that arrive – the first item brought into the centre in Sutton Coldfield was a mini radio – are moved upstairs on a conveyor – helter skelter like in appearance. Goods head up to, in this case, three floors featuring Amazon Robotics where products are then stowed and customer orders picked.
Advertisement
Hide AdAdvertisement
Hide AdThe robots, which power tall yellow shelves around the floors provide a fascinating digital spectacle, almost hypnotic. They use QR codes on the floor to navigate their way around with cameras stopping them colliding.
A couple of times, it was almost as if one member of this futuristic workforce was acting gentlemanly, stopping to allow a fellow robot to pass, with an almost ‘after you’ motion. This technology brings goods to employees to be either stowed or picked for delivery.
FC Lead Sanjeev Gaddu, who has worked at Amazon for three years, says the new centre launch has been positive. "The robotic technology is incredible and the way we are utilising the space in this centre and the amount of units that are coming into the warehouse and being stowed – it’s something that has never been done before here in the UK," he enthuses.
"As a team lead I have to make sure the operation on this floor is working at maximum every single day. We have progressed so much already in a couple of weeks. We are at 30 per cent capacity on head count but once we are operating at 100 per cent we will be hitting volumes that are unbelievable and mouthwatering."
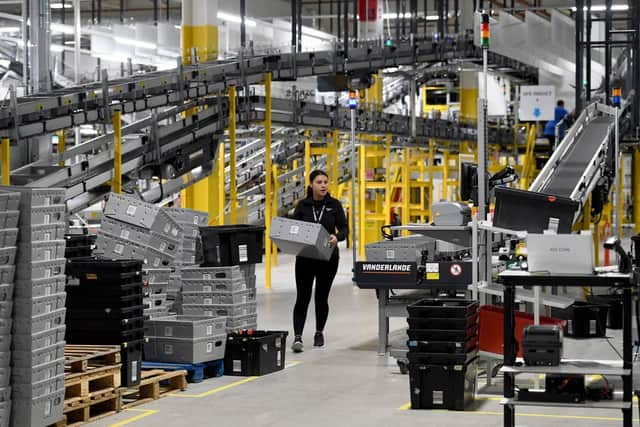
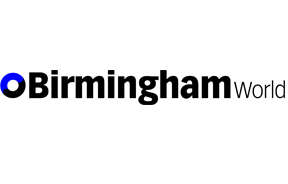
What happens in the packing department at the new Amazon warehouse in Sutton Coldfield?
Advertisement
Hide AdAdvertisement
Hide AdFrom stowing and picking, we head to packing where there are single and multi-pack stations, depending on the customer’s order.
"The technology behind it all is truly unbelievable," says Celia. "The swipe of a hand across a scanner and it lights up a shelf to put the item for packing."
The operation is running smoothly and Celia explains: "We train staff here in all of the different processes. They get variety in the job but it also supports us because employees are skilled to carry out different tasks."
Celia said training is vital and Amazon also provides a Career Choice which is open to employees with a year’s service. Through the scheme, the company will pay up to 95 per cent of tuition and associated fees (up to £8,000 over four years) towards a nationally recognised qualification.
The main hub and ‘Kick Out’ at the new £500m Amazon fulfilment centre in Sutton Coldfield
Advertisement
Hide AdAdvertisement
Hide AdAs we progress through the centre, we walk past a main hub, full of giant screens run by Reliability Maintenance Engineers. "They can look at the flow in the centre, the volume in orders," adds Celia. "It means we can see we have the right people in the right places. "They can see any jams and issues with conveyance that might impact delivery time and they can go and manage that."
After that, we head to the ‘Kick Out’ section and meet Jess Bosley. She started at Amazon in 2020 as a Graduate Area Manager after leaving university and has now worked her way up to Operations Manager.
"In terms of this section of the centre, when we have parcels on the line, they go to shipping," she explains. "But if they fall at ‘kick out’ it means something is wrong with them. It might be the item weighs differently to what it should do, or it is in the wrong box or there is too much or too little packaging. So it comes down and our operators reopen the box, check everything is right and pop it back on the line to shipping."
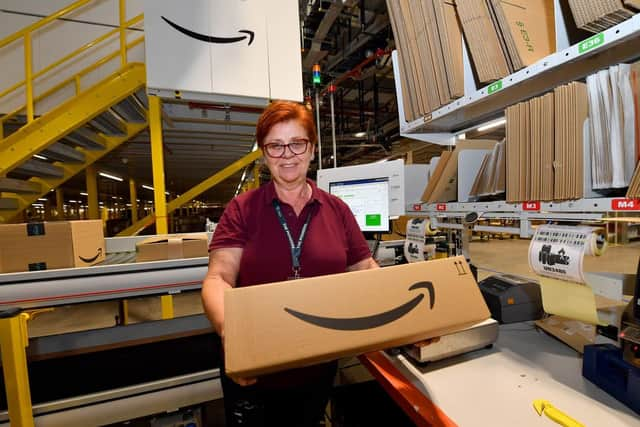
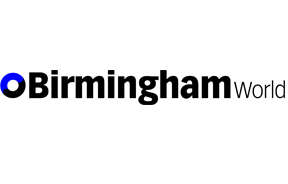
Once an order is picked and packaged, it is put through the SLAM – Scan-Label-Apply-Manifest – machine, another incredible piece of technology
Advertisement
Hide AdAdvertisement
Hide Ad"It does a weight check – to identify issues – and if all is well, within seconds sends a signal to printer," adds Celia. "It prints the label and this is the first time in process where people’s name and address is available. SLAM then blows the label onto the package with compressed air rather than sticking it on in case something fragile is inside."
The final package is then distributed via chutes to the correct delivery carrier, based on areas, before starting its journey to the customer. As we head back, and past the packaging stations, Celia points out: "As we move towards the festive period there will be stations dedicated to gift bags."
What are the plans for Christmas - and Black Friday at the Amazon warehouse in Sutton Coldfield?
And, there, she has mentioned it – Christmas! We are heading into a major period, with Black Friday also imminent. "As we get ready for peak, we will have more people because we have more orders," she says. "There is actually a really good atmosphere in the building on those days.
“We have lots of activities on site, competitions, dress up events, arcade games and beat-the-manager days in the canteen. There’s a lot of energy."
Advertisement
Hide AdAdvertisement
Hide AdAnd, with that, the tour is over. The new site is up and running just in time for that peak period. "We are proud to be under way," says Celia. “They say it takes a community to raise a child. Well it takes a complete network to launch a new site. So many people have come from sites already up and running to support new team members and to train them. You need that huge support and it’s been a huge team effort."
Amazon’s customer fulfilment process
- The majority of products available on amazon.co.uk come from other companies – large, medium and small.
- These products are first sent to one of two receive centres in the UK, one in Coventry, one in Doncaster.
- Products aren’t held at receive centres – the teams at these two buildings distribute the products to Amazon’s network of 30 fulfilment centres, the latest being Sutton Coldfield.
- As soon as the product hits the shelf in the fulfilment centre, customers can click “buy”.
- The customer order is then picked, packed and sent to a sortation centre which looks after a large geographic or postcode area.
- From there, the order goes to a delivery station which looks after a smaller area – and from there it’s delivered to the customer.
Comment Guidelines
National World encourages reader discussion on our stories. User feedback, insights and back-and-forth exchanges add a rich layer of context to reporting. Please review our Community Guidelines before commenting.